La guida si sofferma in particolare sulle procedure di controllo macchine e sulla lockout-tagout.
La regolare manutenzione di ambienti, attrezzature, impianti è una importante misura generale di tutela nei luoghi di lavoro.
Il problema è che le attività di manutenzione di macchine/impianti sono attività che troppe volte sono contrassegnate da infortuni gravi o mortali.
E se una delle più frequenti cause di infortunio nella manutenzione o pulizia di una macchina è la riattivazione non intenzionale o inattesa di fonti di energia, nel proteggere i lavoratori ha particolare efficacia una procedura elaborata dallaOSHA (standard 29 CFR 1910.147), nota come lockout/tagout (LOTO).
Per approfondire questa procedura e per fornire ai nostri lettori altri utili indicazioni e documenti per la sicurezza nelle attività di manutenzione, possiamo fare riferimento ad una guida prodotta dall’ ATS Brianza dal titolo “ Utilizzo in sicurezza delle macchine. Guida per le imprese”, un documento elaborato attraverso il lavoro del gruppo “Sicurezza macchine” costituito nell’ambito del Comitato di Coordinamento Provinciale di Monza e Lecco ex art.7 D.Lgs. 81/08.
Leggi anche:
Le istruzioni per la sicurezza degli addetti alla manutenzione
Attrezzature di lavoro e manutenzione: verifiche periodiche e formazione
Procedura di lockout-tagout e avviamento di una macchina
Nell’Allegato N relativo all’introduzione alla procedura di lockout – tagout si indica che si parla di “avviamento inatteso o accidentale quando si ha la riattivazione di una macchina causata da:
- un comando di avviamento risultante da un guasto del sistema di comando;
- un’azione involontaria su un comando di avviamento o un segnale da un sensore che aziona un comando;
- ripristino dell’alimentazione di energia dopo un’interruzione;
- influenze esterne/interne (gravità, vento, autoaccensione in motori a combustione interna, ecc.) su parti della macchina”.
E le procedure di lockout/tagout (LOTO), benché siano ancora poco applicate, “rappresentano la metodologia più affidabile per effettuare l’isolamento sicuro delle fonti di alimentazione di una macchina e permettono di elevare il livello di sicurezza nella manutenzione, ordinaria e straordinaria, mediante il controllo dell’energia pericolosa”.
Si indica che in linea di principio “la procedura di lockout/tagout richiede che la messa in sicurezza di una macchina o di un impianto avvenga secondo una sequenza preordinata per l’applicazione dei dispositivi di isolamento e di ‘lucchettaggio’”.
In particolare con “lockout” si intende il “posizionamento di un lucchetto in corrispondenza della posizione OFF di un dispositivo di isolamento (sezionatore, valvola, ecc.) di una qualsiasi fonte energetica (energia elettrica, fluido pericoloso, ecc.)”. E con “tagout” si intende “il posizionamento di un cartello o etichetta in corrispondenza del lucchetto usato per il lockout, riportante chiaramente il nominativo dell’operatore autorizzato”.
Riprendiamo dall’allegato una immagine:
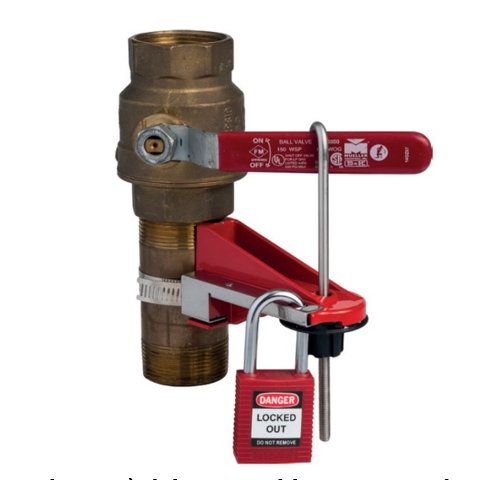
LOTO: i passi fondamentali della procedura
L’Allegato N riporta alcune indicazioni sui passi fondamentali della procedura:
- Identificazione del pericolo: “preliminarmente è necessario identificare le fonti di energia pericolose di macchine/impianti” (energia elettrica, energia elastica, energia potenziale, aria compressa, fluidi in pressione o a temperatura elevata, agenti chimici pericolosi, …). E dopo “aver identificato i tipi di energia da neutralizzare (meccanica, elettrica, pneumatica, etc.) va scelto e preparato il bloccaggio della fonte (chiusura delle valvole, interruzione della corrente, etc.)”.
- Arresto: “arrestare il funzionamento delle attrezzature e dei macchinari interessati secondo la normale modalità di utilizzo”;
- Notifica: “occorre informare tutte le persone interessate che si è in procinto di operare sul macchinario effettuandone il bloccaggio”;
- Bloccaggio: “occorre isolare le fonti di energia con le apparecchiature di sezionamento individuate (es. aprire l’interruttore principale della macchina, staccare la spina o l’alimentazione dalla blindosbarra, chiudere le valvole di intercettazione dei fluidi, inserire puntelli metallici, chiavistelli o blocchi meccanici per evitare la caduta per gravità, etc.). Il bloccaggio deve comportare un blocco fisico per impedire il riavvio dell’impianto. Ogni persona che lavora all’attrezzatura di lavoro disporrà del proprio bloccaggio evidenziato. Se necessario, le tenaglie di bloccaggio possono essere utilizzate per permettere che più lucchetti siano disposti sullo stesso dispositivo che isola l’energia”.
- Controllo e rilascio di energia immagazzinata: “per essere sicuri che il macchinario sia completamente isolato, va eseguito un test su tutti i comandi delle installazioni e dei circuiti elettrici sui quali va eseguito l’intervento e va eliminata ogni energia residua (eliminazione della pressione, scarica condensatori e accumulatori, etc.). Dopo aver controllato che nessuna persona è esposta, va eseguito un tentativo di messa in funzione dell’apparecchiatura con le funzioni di controllo normali, per verificare che la macchina/impianto non funzioni e che tutte le sorgenti di energia siano isolate”;
- Tagout: “procedere all’identificazione del bloccaggio indicando la data e il nome del personale che lo effettua”;
- Rimozione del lockout: “solo al termine dell’esecuzione del lavoro di manutenzione, dopo aver controllato le apparecchiature e tutte le parti collegate fra l’attrezzatura di lavoro e il dispositivo che isola l’energia e informate tutte le persone interessate dal bloccaggio che lo stesso si è concluso, potranno essere rimossi i lucchetti e si potrà rialimentare l’apparecchiatura. Ogni lucchetto potrà essere rimosso soltanto dall’operatore indicato sulla Tag”.
Esempio di procedura di controllo e manutenzione macchine
Facciamo cenno poi anche all’Allegato O che presenta un fac-simile di una procedura di controllo e manutenzione macchine.
La “Procedura di controllo e manutenzione macchine” presentata ha lo scopo di “definire le modalità con cui viene gestita l’attività di manutenzione ordinaria e straordinaria” e si applica “a tutte le operazioni di manutenzione su macchine e attrezzature presenti in azienda a disposizione degli operatori.
Si indica che la pianificazione ed effettuazione degli interventi di manutenzione si può articolare in tre fasi:
- Fase 1 – Periodicità e individuazione degli elementi da sottoporre a manutenzione: periodicità e elementi “sono definiti dal Datore di Lavoro sulla base di quanto indicato sul manuale d’uso e manutenzione della macchina (ove presente) ma anche sulla base dell’esperienza diretta fornita da lavoratori e preposti, della vita residua del macchinario, della valutazione dei rischi e tenendo conto dei possibili ‘utilizzi non corretti ma ragionevolmente prevedibili’;
- Fase 2 – Modalità di controllo e manutenzione: “il Datore di Lavoro, anche sulla base di quanto indicato nel libretto d’uso e manutenzione, stabilisce in che modo mantenere in efficienza i componenti e le condizioni di sicurezza identificate precedentemente”. E le modalità possono essere le seguenti: a) “verifica dell’assenza di alterazioni dei componenti di sicurezza (ad esempio, controllo dell’integrità del carter protettivo e del relativo dispositivo di interblocco)”; b) “controllo del funzionamento (ad esempio, con il macchinario funzionante, osservare se lo scorrimento del nastro sulle guide avviene normalmente, senza inceppamenti)”; c) “intervento manutentivo (ad esempio, lubrificazione delle guide, sostituzione nastro)”. Ed è poi necessario “descrivere la procedura da seguire nel caso i controlli e le manutenzioni dovessero far emergere guasti o anomalie”.
- Fase 3 – Individuazione dei soggetti: “le attività di manutenzione ordinaria e straordinaria sono in capo al Datore di Lavoro che designa formalmente lavoratori adeguatamente formati e addestrati per svolgere effettivamente i compiti di manutenzione e controllo. In caso di interventi più complessi e particolareggiati (ad esempio, manutenzione e controllo di componenti elettriche o guasti) l’attività di manutenzione ordinaria o straordinaria può essere affidata ad aziende o soggetti esterni specializzati”.
Si indica poi che tutti gli interventi ordinari e straordinari (escluso quelli previsti quotidianamente) “verranno registrati sulla “Scheda di controllo e manutenzione macchina” (“viene istituita per ogni macchina una Scheda Manutenzione. Su tale scheda vengono registrati gli interventi di manutenzione programmata e a guasto”). Un esempio di scheda è presentato nell’Allegato.
Concludiamo segnalando che nell’Allegato è riportato anche un fac-simile di “Piano di controllo e manutenzione” (“viene istituito un piano di controllo e manutenzione dove si definiscono le componenti da sottoporre a manutenzione, la tipologia di intervento, le procedure in caso di anomalia, gli esecutori e la frequenza di manutenzione”).
Ne riprendiamo uno stralcio:
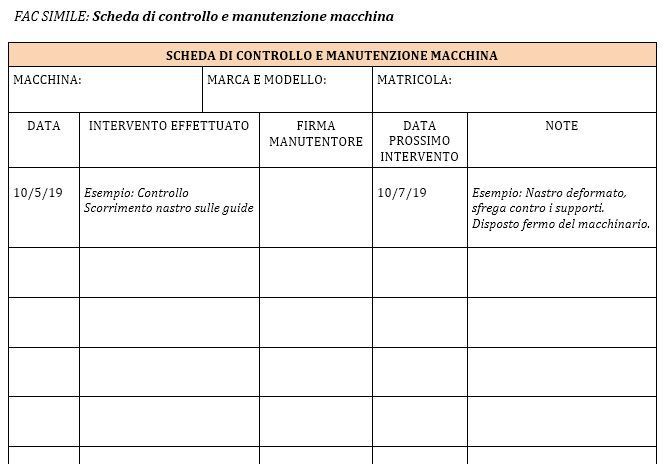
Nel Piano di controllo e manutenzione presentato è annotato che si consiglia di non usare la scheda “per registrare eventuali controlli/manutenzioni giornalieri. Per dimostrare la loro effettiva esecuzione è più utile, infatti, poter dimostrare che il personale incaricato è stato adeguatamente formato e addestrato su quali interventi devono essere giornalmente effettuati sullo specifico macchinario”.
Segnaliamo in conclusione che la procedura può essere distribuita “al Responsabile della Manutenzione ed a tutti gli incaricati della manutenzione designati dal Datore di Lavoro”.