Focus sui fattori e le dinamiche che possono provocare incidenti e sulle possibili misure di prevenzione per tutelare la salute dei lavoratori.
Riguardo ai dati infortunistici anche nei settori della fabbricazione di prodotti chimici e della fabbricazione di articoli in gomma e materie plastiche (codici C20 e C22 della classificazione Ateco 2007) non sono pochi gli infortuni gravi e mortali che avvengono ogni anno.
Per questi due settori l’analisi delle dinamiche infortunistiche presenti nell’archivio di Infor.Mo, sistema di sorveglianza nazionale degli infortuni mortali e gravi sul lavoro, nel periodo 2002 – 2019 mostra la presenza di 152 infortuni gravi e mortali (di cui 17 in eventi collettivi) “a cui sono collegati 284 fattori di rischio identificati con il modello di analisi multifattoriale”. E se nel periodo 2016 – 2019 “si rileva una diminuzione degli eventi riconosciuti positivi”, c’è una “contrazione però inferiore alla media del complesso di settori appartenenti al Manifatturiero”.
A ricordarlo, fornendo anche dati relativi ai primi mesi del 2022, è una recente scheda (scheda 19) prodotto da Infor.MO (Inail) e dal titolo “ Fattori causali e dinamiche infortunistiche nella fabbricazione di articoli in gomma, materie plastiche e prodotti chimici”.
Leggi anche:
Sostanze chimiche reprotossiche: l’Inail ne analizza i rischi
Microplastiche nei tessuti, ecco il rapporto dell’Agenzia Europea per l’Ambiente
La scheda – a cura di M. Pellicci, A. Guglielmi, D. De Merich, L. Bolognini, G. Cenci, G. Rucci e P. Tittarelli – non analizza solo i dati relativi alle dinamiche infortunistiche, ma si sofferma anche sui fattori di rischio e su alcune misure preventive e protettive da adottare per il controllo e la gestione del rischio infortunistico nella produzione di articoli in gomma e materie plastiche.
La scheda n.19 di Informo e i principali fattori di rischio
Riguardo ai fattori di rischio il documento si sofferma sulle specificità dei fattori causali alla base degli eventi gravi e mortali presentati nella scheda.
Riprendiamo una tabella con la distribuzione dei fattori di rischio:
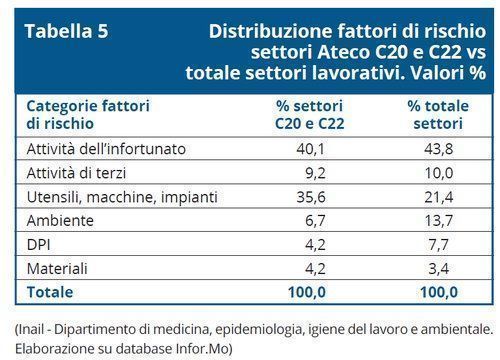
Si indica che al primo posto (49,3%) ci sono “gli aspetti procedurali (attività infortunato e di terzi), riassumibili in usi errati di attrezzatura o in sequenze operative errate, per pratiche abituali (42,2%), azioni estemporanee (28,9%) e carenza di informazione/formazione / addestramento (24,1%)”.
E in particolare le criticità procedurali sono collegate a “interventi operativi con organi, macchine o impianti in funzione, modalità scorrette di posizionamento (rispetto a organi, macchine e loro componenti in movimento, in zone in quota), riavvio e conduzione di impianti e mezzi senza coordinamento con altri lavoratori presenti nell’ambiente o in zone di pericolo”.
Riguardo poi alla categoria degli utensili, macchine e impianti implicati negli eventi “si evidenzia la mancanza o l’inadeguatezza di protezioni fisse/mobili e sensibili (62,6%) nonché l’assenza di accessori di sicurezza, di sistemi quali sensori di pressione e temperatura e di manutenzione (23,1%), con conseguenti problemi strutturali delle macchine/attrezzature / impianti in uso. Si tratta essenzialmente di macchine di lavorazione della gomma/plastica e di impianti di processo/fabbricazione di derivati e semiderivati chimici”.
Nel fattore Ambiente emergono poi gli “spazi non adeguati per le lavorazioni anche in termini di viabilità, l’assenza di sistemi di aspirazione e ventilazione e la presenza di microclima non adeguato”.
Infine i problemi di sicurezza registrati per i dispositivi di protezione individuale (DPI) sono “riconducibili alla non fornitura di dispositivi o, in misura inferiore, al non utilizzo di DPI di protezione delle vie respiratorie, sistemi di imbrago anche per il recupero in emergenza, visiere, occhiali e guanti mentre per la categoria dei materiali, più frequente della media di tutti i settori, ricorre lo stoccaggio non adeguato sia per modalità che per incompatibilità dei prodotti e in misura inferiore le caratteristiche di pericolosità dell’agente chimico utilizzato”.
Rimandiamo alla lettura della scheda che si sofferma anche su altri rischi ( cadute dall’alto di gravi, sviluppo di fiamme, …).
Misure preventive e protettive: il rischio macchina e le cadute dei gravi
Riguardo alle misure di prevenzione si indica che per il contatto con organi lavoratori negli interventi su macchine in fase di lavorazione per inceppamenti, regolazioni, registrazioni e manutenzione, “occorre garantire che le parti meccaniche in movimento e le relative zone di operazione siano protetti o segregati oppure provvisti di dispositivi di sicurezza; nel caso in cui per esigenze di lavorazione, ciò non sia possibile, limitare al minimo indispensabile le parti in movimento o le zone di operazione non protette e adottare misure alternative di riduzione del rischio”.
Altre indicazioni:
- “dotare gli operatori di abiti da lavoro e di DPI anti-impigliamento;
- divieto di avvicinarsi alla macchina prima che tutti i suoi componenti si siano arrestati;
- pianificare una regolare manutenzione delle apparecchiature e garantire che gli interventi di manutenzione o riparazione siano eseguiti da personale autorizzato e specializzato;
- rimettere al loro posto la protezione o il dispositivo di sicurezza alla fine dell’intervento di manutenzione;
- prevenire la manomissione dei dispositivi di protezione (es. montaggi in posizione nascosta o non raggiungibile, saldature, viti non smontabili, rivettature o sistemi di monitoraggio e controllo);
- garantire il corretto trasferimento delle procedure lavorative”.
Riguardo, invece, alle cadute dall’alto di gravi, che avvengono durante la manutenzione o il controllo di impianti o strutture in altezza e nella movimentazione di materiali sfusi o in contenitori, è bene:
- “interdire al passaggio e allo stazionamento le aree sottostanti le attività;
- fornire attrezzature ancorabili a chi opera in altezza;
- prevedere se necessario, l’utilizzo di movieri e di segnalazioni fisse o mobili”.
Misure preventive e protettive: incendi, caduta dall’alto e agenti chimici
La scheda 19 riporta anche indicazioni per i rischi connessi allo sviluppo di fiamme:
- verificare che lo stoccaggio di materie prime incompatibili sia eseguito in modo da garantire un idoneo isolamento tra esse anche in caso di sversamento accidentale (vasche di contenimento, verifica percorsi fognari non coincidenti);
- rimuovere (con verifica assenza) tutti i materiali infiammabili nella zona di esecuzione manutenzioni elettriche;
- prevedere la messa a terra (con verifica periodica) di tutte le parti fisse metalliche, macchine, impianti, attrezzature presenti nelle zone con presenza di sostanze infiammabili;
- limitare la formazione di atmosfere infiammabili e le fonti di innesco anche con l’uso di indumenti anti-scintilla;
- verifiche periodiche sui sistemi di controllo della temperatura nei processi termici molto vicini alle temperature di autoaccensione delle materie utilizzate;
- utilizzo di attrezzature e impianti adeguati;
- informazione e formazione specifica sul corretto uso di prodotti infiammabili”.
La scheda si sofferma anche sulla caduta dall’alto o in profondità dell’infortunato:
- nelle fasi di manutenzione/controllo/ pulizia di impianti o strutture in altezza o in profondità verificare la presenza e il corretto uso dei dispositivi di protezione collettiva contro la caduta dall’alto;
- utilizzare i DPI anticaduta con ancoraggi certificati UNI EN 795;
- verificare l’idoneità dei lavoratori (formazione, addestramento, idoneità sanitaria specifica);
- utilizzare idonei mezzi di accesso in altezza”.
Invece per la fuoriuscita/contatto con gas, fumi, aerosol e liquidi (alta/bassa temperatura, pericolosi):
- verificare il completo svuotamento con eliminazione di sovrappressioni e temperature pericolose dell’impianto durante le fasi di carico e scarico o prima di iniziare l’attività di manutenzione;
- nelle zone a rischio sovrappressioni dotare gli impianti di manometri di controllo regolarmente manutenuti;
- dotare i manutentori di termometro a infrarossi per il controllo a distanza della temperatura;
- regolare manutenzione delle attrezzature, macchine e impianti utilizzati inclusi gli accessori di sicurezza (sensori di temperatura, pressione, ecc.);
- predisporre impianti di aspirazione localizzata e impianti di ventilazione adeguati alle lavorazioni;
- predisporre adeguate misure e procedure lavorative a garantire il loro trasferimento tramite la formazione e informazione;
- vigilare sulla reale applicazione delle procedure lavorative nel rispetto di quanto indicato nella scheda dei dati di sicurezza (SDS);
- corretto uso dei DPI”.
Si ricorda poi che l’attuale normativa in materia di rischio da agenti chimici “è rappresentata dal Titolo IX, capo I del d.lgs. 81/2008 e che l’emanazione del d.lgs. 39/2016 implementa gli obblighi del regolamento CE n. 1907/06 (REACH) e del regolamento CE n. 1272/08 (CLP). Tali aggiornamenti forniscono importanti fonti di informazione e integrano gli obiettivi di tutela della salute e della sicurezza incentivando la ricerca e lo sviluppo di processi e sostanze meno pericolosi”.
Rimandiamo, anche in questo caso alla lettura integrale della scheda che riporta indicazioni per prevenire gli infortuni conseguenti all’avviamento inatteso delle macchine e ulteriori dettagli su quanto previsto dai Regolamenti REACH e CLP.